Manufacturing
Our headquarters, located in Raynham, MA, was custom built in 2008 for the sole purpose of high quality battery manufacturing. The 82,000 sq. ft. facility was specifically designed for optimal safety and material flow throughout the production process.
State-of-the-Art Facility
- Designed-in safety controls including fortified infrastructure and automated event isolation chamber system ensure operational safety and continuity
- Dedicated design engineering, advanced R&D, rapid prototyping, and testing laboratories
- Highly secured and controlled environments for protection of our people and products
- Set on a 20-acre site providing the ability for future expansion
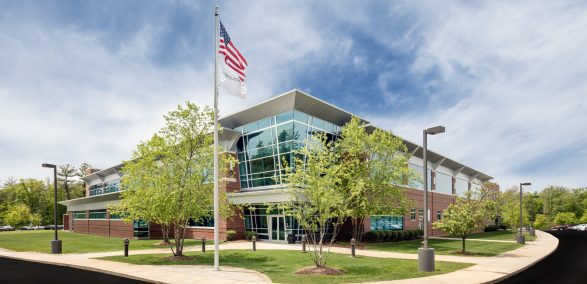
Broad Manufacturing Capabilities
- Core Product Capabilities: Primary lithium cells, primary battery packs, high temperature ultracapacitors
- Key Technical Capabilities: Cathode and electrolyte mixing/production, IPC610 soldering, laser welding and marking, glass-to-metal seals, ultrasonic and resistance welding, automated assembly
- Strong operational excellence through utilization of lean manufacturing systems
- Vast portfolio of technical capabilities, intellectual capital, and industry experience ensuring the ability to meet all project requirements
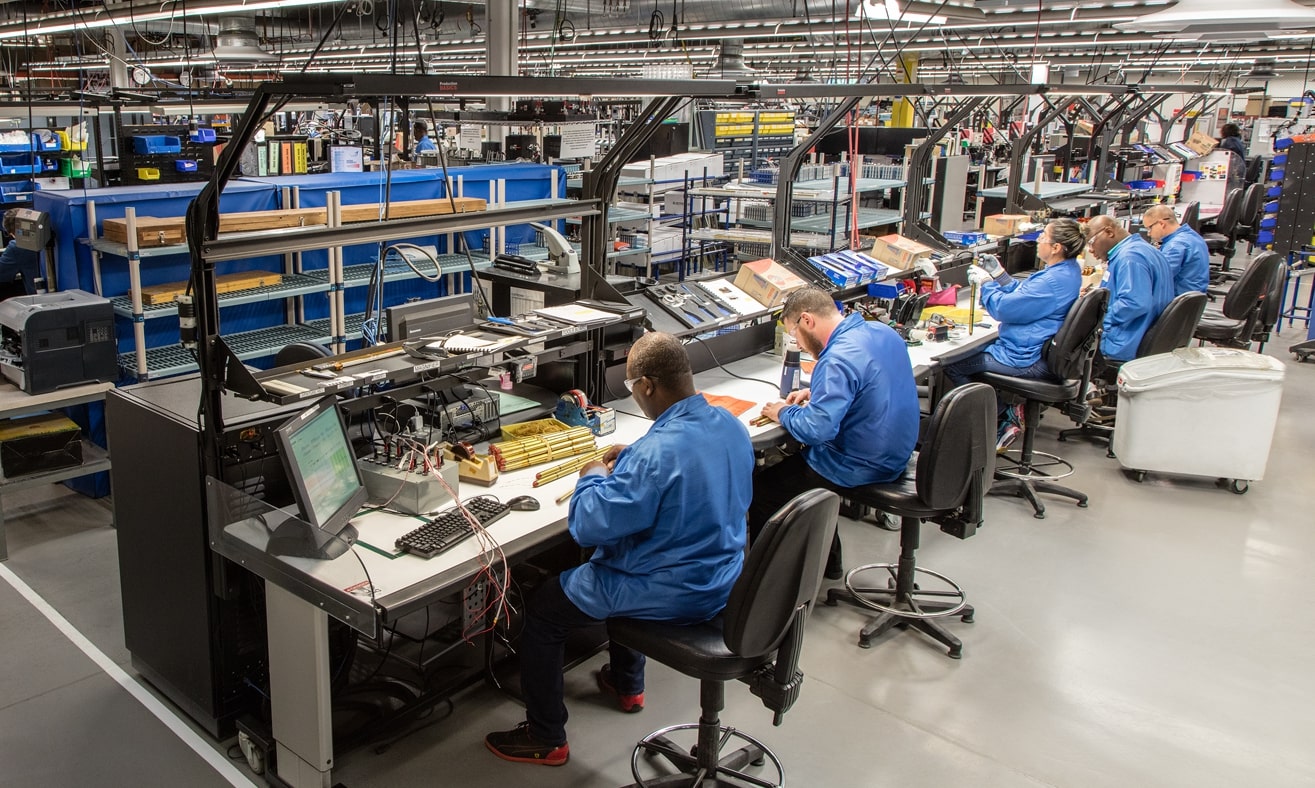
Security of Supply
- Business Recovery Plan: In the event of a disaster or catastrophic event, a comprehensive business recovery plan is maintained; critical, redundant equipment is stored offsite for expedited resumption of full production
- Supplier Management Process: Ensures the uninterrupted flow of incoming materials and required services
- Risk Assessments: Regularly conducted to ensure adequate controls are in place and all potential scenarios are evaluated
- Designed-in safety controls and redundant facility infrastructure
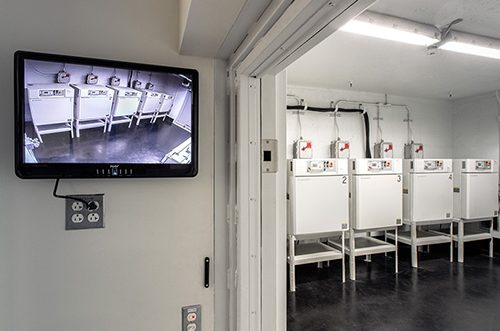
Quality
- Quality System Certification: ISO 9001:2015 registered facility
- Electrical Testing: Over 500 Maccor electrical testing channels available for production sampling, analysis and evaluation, and customer specific testing requirements. 100% of Electrochem® manufactured cells tested for open circuit voltage and closed circuit voltage prior to shipping.
- Dimensional Measurement: Rigorous test method validation protocols for critical features through the use of coordinate measuring machines, optical measuring devices, specialty gauges and handheld devices
- In-house X-Ray capability: Enables safe, nondestructive analysis for standard product verification or for more complicated field failure analysis
- Materials Lab: Metal and alloy grain analysis, micro-hardness testing, electron dispersive spectroscopy (EDS), ionic chromatography, specialty materials testing and other destructive and nondestructive types of analysis
- Troubleshooting Analysis: Employ ASQ Root Cause training, Kepner-Tregoe, and Six Sigma analytical troubleshooting techniques
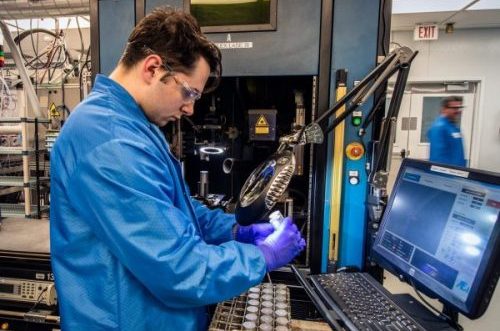
Safety-Based Culture
- Eagle Eye: An associate driven feedback process focusing on quality and safety improvements
- Behavioral Based Safety Program: Associate driven observation program focused on promoting proactive safe behavior before incidents or near misses occur
- Process Safety Management: A systematic detailed approach to manage and reduce the severity of incidents in the handling and processing of hazardous chemicals
- Emergency Response Team: Fully staffed on-scene, all-hazards incident management team. As members of the community we not only partner with local First Responders, we also provide yearly training in Battery Emergencies.
- Electrochem strictly adheres to numerous health, safety, and security rules and standards, including but not limited to:
- International Traffic in Arms Regulations (ITAR)
- Department of Homeland Security (DHS)
- OSHA Process Safety Management (PSM)
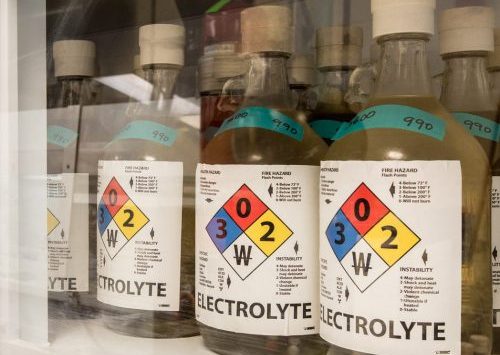